Viaje a las tripas de la única fábrica de trenes de Cataluña
La planta de Alstom de Santa Perpetua de Mogoda tiene entre manos el mayor proyecto de la historia del ferrocarril en España
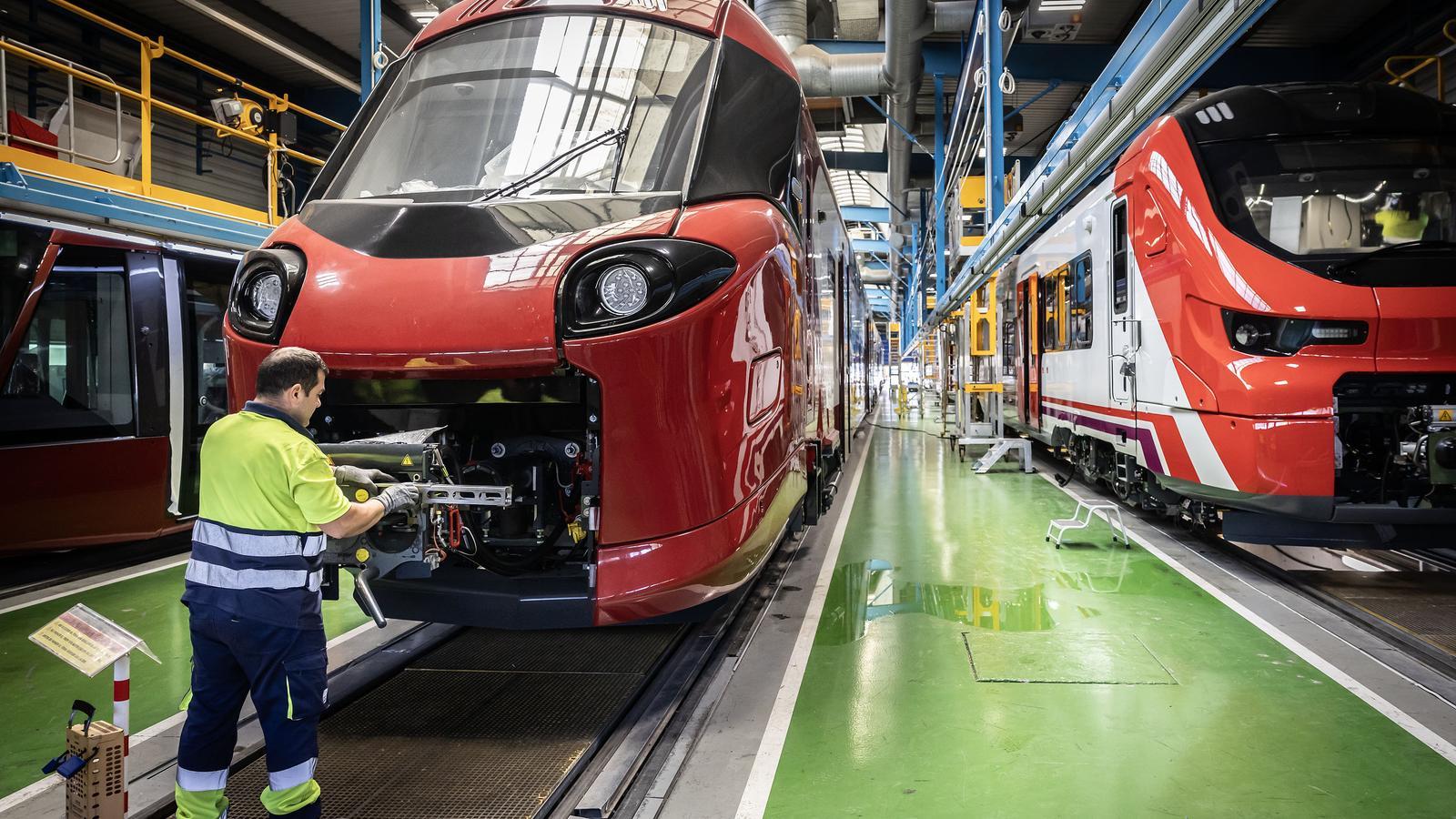
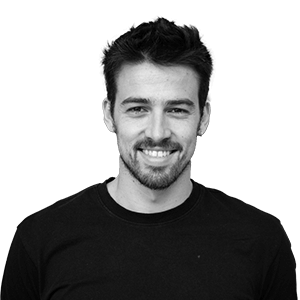
BarcelonaNo existen dos vías iguales. Ni siquiera los raíles de una misma vía férrea tienen la misma distancia. Es cosa de particularidades físicas de cada territorio. También de sus condiciones socioeconómicas: incluso hay pueblos que carecen de estación porque así lo decidieron sus vecinos. El tren traería gente pobre, decían.
Estas particularidades quedan impresas en toda la estructura ferroviaria, también en la frecuencia de las paradas y en los trenes y metros que, día tras día, bombean a miles de ciudadanos por pueblos y ciudades. En una fábrica situada en las afueras de Barcelona, todos estos detalles reposan a pocos metros de distancia. Tres vehículos de propulsión eléctrica sobre raíles de gran tonelaje son testados por decenas de operarios a contrarreloj. Tienen que cumplir con los plazos de contratos millonarios.
Uno es un tranvía de una sola cabina, pensado para ser ensamblado con otro vehículo idéntico; el otro es un tren regional, ideado por recorrer grandes distancias entre estaciones, y el tercero es un ejemplar de un contrato milmillonario para fabricar más de 200 trenes de alta capacidad. Los tres concentran en la separación de las ruedas, el número de coches y la amplitud de las puertas, entre otros muchos detalles, las particularidades de un lugar en concreto. Son tres países diferentes aparcados uno junto a otro.
Están en la nave de pruebas de la única fábrica de trenes de Cataluña, que está ubicada en Santa Perpètua de Mogoda y tiene una historia centenaria. Pertenece a Alstom, una compañía francesa que en 1989 adquirió La Maquinista Terrestre y Marítima, fundada en 1855. Justo hace 30 años, Alstom inauguraba el centro industrial que hoy funciona a pleno rendimiento para seguir produciendo tranvías, metros y trenes para todo el mundo, mientras da cabida a los más de 200 trenes que le ha encargado Renfe, el operador ferroviario público español. Se trata del mayor contrato ferroviario de la historia del ferrocarril en el Estado. La planta se expande en más de 360.000 metros cuadrados encajonados entre la C-59 y Mollet del Vallès, y acoge a más de 1.000 trabajadores, el doble que hace tres años.
La compañía se adjudicó un proyecto de 152 trenes en marzo de 2021 y otro de 49 a finales de 2022, lo que elevó el encargo de fabricación de Renfe a 201 trenes por valor de 1.800 millones de euros . Todos ellos se fabricarán en esta planta, que para este encargo ha tenido que modernizarse con una inversión sin precedentes y ha tenido que crear el mayor taller automatizado del grupo. La línea de acabados es completamente nueva. Serán trenes de alta capacidad, de 100 metros de longitud para llevar a 900 pasajeros, y mixtos, es decir, alternarán coches de uno y dos pisos. Son de la gama Coradia, una marca protegida del grupo francés que circula desde hace décadas en una decena de países.
"Es como un autobús urbano", explica al ARA Miguel Angel Martín, el director del proyecto de gran capacidad para Renfe, mientras mira el nuevo modelo, que entregarán a finales de año. El contrato también incluye el mantenimiento de estos trenes durante 15 años, que llegan para transportar al menos a un 20% más de pasajeros por hora en las redes de Cercanías más congestionadas, como Madrid y Barcelona. Este gigante francés no sólo fabrica trenes, sino que también realiza servicios de mantenimiento y suministra sistemas de señalización, seguridad y control. En toda España existen cuatro grandes fabricantes de material rodante: Stadler, Talgo, CAF y Alstom.
Detrás del diseño de este tren hay una red viaria antigua con unas limitaciones determinadas y una distribución de estaciones particular: fuera de la ciudad son trenes regionales, pero una vez entran en ciudades como Barcelona esta nueva hornada debe adaptarse a una mayor frecuencia de paradas, similar a la de un metro. Y esto hace que los nuevos trenes tengan que acelerar como un tren suburbano, que sea ligeramente más lento que un regional cualquiera, también que cuente con muchas puertas, así como un espacio de entrada más amplio para ganar tiempo en cada parada: cómo menos tarde el usuario en bajar o subir, menos tiempo se perderá en las estaciones. Otra novedad respecto a los trenes actuales, los de la plataforma X'Trapolis, es que los coches son más anchos y que las baterías se montan en el techo para rebajar la altura del tren. Si hay menos escalones, se tarda menos en acceder, y si está más cerca del andén es más fácil entrar. Asimismo, los coches de los extremos son más diáfanos, ya que es donde se concentra la gente para salir más rápidamente de la estación. La puntualidad comienza en el diseño industrial.
Lo cierto es que en las peticiones del contratista existen las virtudes y carencias de la estructura ferroviaria, pero un denominador es conseguir trenes el máximo de ligeros con la máxima adherencia. Esto explica que estén hechos de aluminio y no de acero. Pese a menos, consumen menos energía, y teniendo en cuenta que la vida útil es de 40 años, la diferencia puede ser de cientos de miles de euros al cabo de las décadas. En el caso de Renfe, todas estas características de trazado, visibles en el diseño de los trenes, buscan maximizar el número de trenes a la hora. Otro elemento importante es el gálibo, el tamaño máximo del vehículo para que pueda pasar por todos los tramos de la vía. De hecho, hace un año el ministerio de Transportes cesó a responsables de Renfe y Adif por un error de los gálibos de la infraestructura en la declaración sobre la red de Adif. Mientras que en el sector aeronáutico todo está pensado para que, pase lo que pase, el avión siga volando, en el transporte ferroviario es lo contrario: si hay problemas, el tren debe poder pararse, excepto cuando está dentro de un túnel . Uno de los peligros, con tanto cableado, es el fuego, por lo que cuentan con una normativa muy específica.
Junto a este tren imponente, de los más modernos de Europa, reposa otro Coradia. "Este otro es como un autobús de línea", explica Martín. Se trata también de un contrato con un operador público, en cuyo caso valorado en 360 millones de euros, para la entrega de 34 trenes regionales de doble piso. Vehículos de 160 metros de longitud que podrán alcanzar una velocidad máxima de 160 kilómetros por hora, pensados por distancias más largas entre estaciones. Tienen asientos más cómodos y mesas en medio. El contratista es el operador luxemburgués CFL y los trenes circularán en la red nacional, así como en Bélgica y en Francia.
El tercer vehículo es un tranvía que circulará por las calles de Casablanca, en Marruecos, y se fabricará en mucho menos tiempo que los otros dos vehículos. Su particularidad es que se trata de un tranvía de una cabina, que circulará con otro vehículo idéntico ensamblado por detrás, algo poco habitual en el sector. Mientras un tren de Cercanías puede recorrer todas las fases de fabricación en cuatro meses, un tranvía ultima el proceso fácilmente en dos semanas. También es distinto el proceso de fabricación: las cajas -los coches antes de ser montados- se equipan antes con todos los accesorios. Los tres, hechos a base de aluminio, llegan a la planta en forma de perfiles extorsionados de aluminio, que se sueldan para formar los distintos subconjuntos de la estructura de la caja, es decir, el techo, las paredes y el vestuario. Se trata de la fase de calderería y mecanizado, la primera de un proceso que termina con la llamada bajada a bogis, que consiste en ensamblar los coches en una estructura rodante de acero, generalmente de dos pares de ruedas, que encajarán en los raíles de las vías.
Un gran robot de soldadura
Estas partes pasan por un pórtico de soldadura automatizada, un robot de gran tamaño que ha permitido optimizar el proceso de soldadura hasta precisiones milimétricas, del que sale la estructura del coche sin pintar, llamada caja en blanco. "Si la montaña no va a Mahoma, Mahoma irá a la montaña", explica al ARA un trabajador de la planta, en referencia a que son las prendas las que se desplazan hasta el soldador a través de vehículos guía automatizados. No es una montaña, pero sí una imponente estructura en forma de pórtico que se desplaza por encima de las partes, y también las cajas una vez montadas, y las va soldando.
Una vez hecha la caja, ésta se envía a pintura, donde se prepara la superficie y después se pinta, y queda lista para el proceso de acabados, que consiste en montar todos los elementos para que el cubículo rectangular soldado y pintado se convierta en un coche de pasajeros. Se le añaden los cofres de tracción, que adaptarán el voltaje de la energía de la catenaria al funcionamiento eléctrico del tren: desde el motor hasta otros elementos del interior. A continuación, se le añaden las puertas, cableado y canales de aire acondicionado. Todas estas piezas reposan en la misma fábrica o en un almacén que tiene la compañía en la Llagosta. "Todo está pensado para que no haya tiempos muertos", explica al ARA el responsable de Alstom en Catalunya, Sergio Boya.
Pese al elevado nivel de sofisticación tecnológica, la revisión de un ojo entrenado con los años es necesaria para que todo funcione. Ocurre en la fase de calderería cuando se aplica calor a las piezas –el ingeniero de soldadura debe prever cómo se deformarán los materiales–, pero también a la hora de medir las dimensiones definitivas de la caja. A pesar de contar con láseres para medir ciertos materiales, no ha decaído todavía una técnica de toda la vida: los trabajadores más experimentados lanzan un hilo de nylon tensado para verificar que las dimensiones están en las tolerancias. Entonces tiene lugar la verificación de cableados –por cada metro de tren hay un kilómetro de cable– y finalmente la bajada del coche a locos. La distancia que separa las ruedas se realiza teniendo en cuenta el ancho de vía que tenga un territorio, que en España, llamado ibérico, es mayor que en el resto de Europa, llamado ancho internacional, y que el ancho métrico. La planta de Alstom tiene las tres vías para realizar pruebas de circulación con diferentes anchos de vía y diferentes niveles de tensión, donde prueba el primer ejemplar de cada serie.
Alstom puede fabricarse en los tres formatos, ya que no sólo exporta tranvías y trenes regionales, sino también metros y trenes de alta y muy alta velocidad. La planta de Santa Perpetua ha enviado metros a Singapur, Varsovia, Shanghai, Panamá, Santo Domingo, Lima y Washington, entre otros. En cuanto a los tranvías que salen de Alstom, algunos a base de acero, han viajado hasta Colonia, Atenas, Montpellier, San Petersburgo, Rabat, Orán, Constantina, Buenos Aires, Qatar y Sydney. Actualmente, en las líneas de la fábrica hay en construcción 126 tranvías para Colonia, 58 para Fráncfort, 80 para Casablanca y tres para Barcelona; estos últimos adaptados para circular por la unión de la Diagonal, que en vez de pantógrafo tendrán un patín para captar la energía de las vías. "De 2009 a 2019, el mercado local estaba prácticamente muerto, fue por la crisis. No había concursos de nuevo material, fue una época durante la que hicimos muchos metros para Sudamérica", explica Boya. De hecho, haber hecho metros para Barcelona –ahora la planta tiene 50 en marcha– les abrió la puerta para exportar a sitios como Panamá y Santo Domingo. La inmensa mayoría de contratos de fabricación que llegan a Santa Perpètua son de operadores públicos. En nuestro país, Alstom también suministrará 10 trenes regionales Coradia a Ferrocarrils de la Generalitat (FGC) para conectar Barcelona con el aeropuerto.
En los próximos meses, los tres vehículos de propulsión eléctrica que reposan en la sala de pruebas de esta planta se enviarán a Marruecos, a Luxemburgo ya manos de Renfe, y se añadirán a la flota de material rodante que Alstom tiene repartida en todo el mundo y que, cada día, bombea a 80 millones de pasajeros.